Concrete is one of the most widely used construction materials, but traditional concrete has a major weakness: it’s prone to cracking under stress. That’s where fiber-reinforced concrete (FRC) comes in.
By adding fibers, such as steel, carbon, glass, or synthetic materials, engineers can significantly enhance concrete strength, durability, and crack resistance. Whether it’s for heavy-duty industrial floors, earthquake-resistant structures, or sleek architectural designs, FRC offers a versatile and high-performance solution.
In this article, we’ll explore the different types of fiber-reinforced concrete, their advantages and disadvantages, and their key applications in modern construction.
What Is Fiber Reinforced Concrete?
Fiber-reinforced concrete is a concrete mixture that contains fibrous materials, which can be steel, glass, synthetic, or natural fibers. These fibers act like a “skeleton” inside the concrete, helping to hold cracks together and prevent them from spreading.
Just like mixing grassroots into soft soil can stop the soil from breaking apart, fibers greatly improve the concrete’s ability to resist cracking, increase its toughness, and make it stronger against impacts. This type of concrete is often used in roads, tunnels, and industrial floors—places that are prone to cracking or need extra durability.
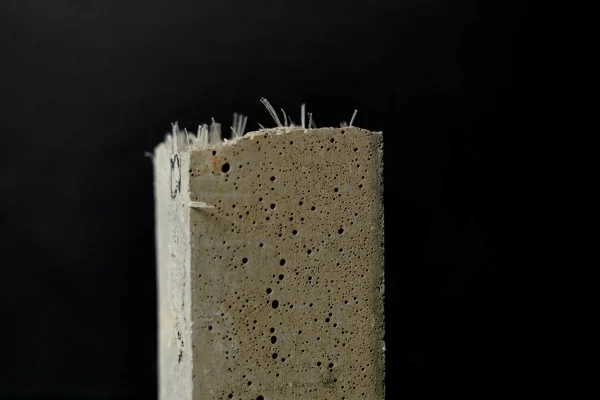
4 Common Types of Fiber Reinforced Concrete
Fiber-reinforced cementitious materials can be classified based on the type and amount of fibers used. Here are some common types of fibers and their characteristics:
1. Steel Fiber-Reinforced Concrete
These materials are known for their high strength and toughness. Adding steel fibers significantly enhances the tensile strength and durability of concrete, improving its resistance to impacts and seismic forces. This makes them ideal for use in bridges, industrial floors, and other structures that need to support heavy loads.
2. Carbon Fiber-Reinforced Concrete
Carbon fibers are lightweight and strong, offering excellent corrosion resistance and high stiffness. The inclusion of carbon fibers boosts the flexural strength and fatigue life of concrete, resulting in outstanding durability and seismic performance. They are particularly suitable for reinforcing high-performance buildings and bridges.
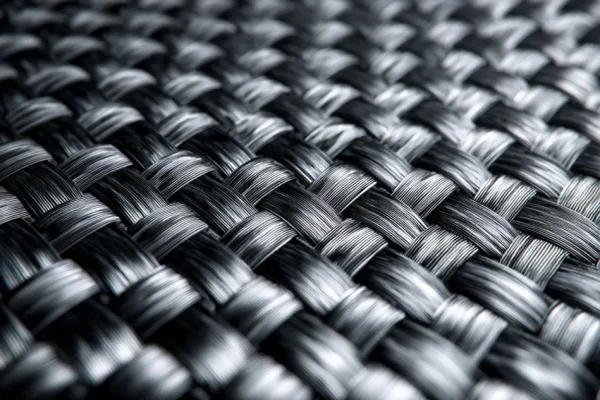
3. Glass Fiber-Reinforced Concrete
Glass fiber-reinforced materials are popular for their lightweight nature, corrosion resistance, and ability to withstand high temperatures. Glass fibers enhance the tensile strength and seismic capacity of concrete, making them widely used in building facades, precast components, and applications requiring insulation.
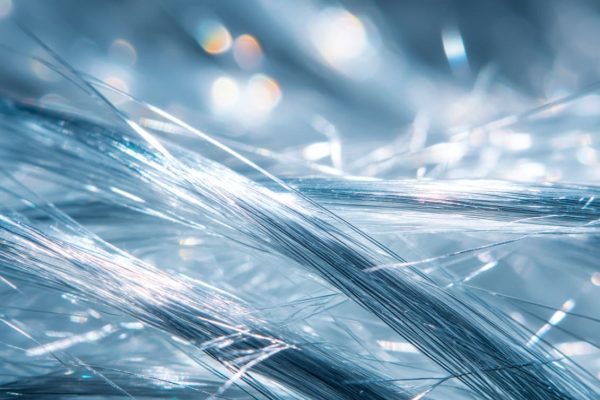
4. Polypropylene Fiber-Reinforced Concrete
Polypropylene fibers are known for their good elasticity, corrosion resistance, and waterproof properties. Their addition significantly improves the crack resistance and impermeability of concrete, resulting in excellent durability and weather resistance. These materials are suitable for roads, floors, and waterproofing projects.
Why Use Concrete Fiber Additives?
Advantages of Fiber-Reinforced Concrete
- Stronger and Tougher: Adding fibers to concrete makes it stronger and more flexible. This helps the concrete resist breaking or cracking under pressure.
- Better Crack Resistance: Fibers help control small cracks from spreading, which keeps the concrete in good shape for a longer time.
- More Durable: Fiber-reinforced concrete can handle impacts, earthquakes, and harsh weather better than regular concrete. It’s a good choice for tough environments.
- Lower Maintenance Costs: Since it’s more durable and less likely to crack, structures made with fiber-reinforced concrete usually need fewer repairs, saving money over time.
- Versatile Use: This type of concrete can be used in many types of construction, like bridges, floors, walls, and waterproofing projects.
Disadvantages of Fiber-Reinforced Concrete
- Higher Cost: It’s generally more expensive to produce than regular concrete, especially when using high-quality fibers.
- Harder to Work With: Mixing the fibers evenly and getting the right consistency requires more skill and care during construction.
- Uneven Quality: If the fibers aren’t spread evenly, the concrete might not perform well, and its strength and durability could be affected.
- Limited Standards: In some places, the rules and guidelines for using fiber-reinforced concrete are still developing, so extra care is needed when designing and using it.
Pros and Cons of Different Types of Fiber-Reinforced Concrete
Fiber Type | Pros | Cons |
Steel Fiber | • High toughness & tensile strength • Good crack resistance | • Hard to mix (fibers clump) • Poor workability, hard to pump • Heavy, uses lots of steel (expensive) • Can rust |
Glass Fiber | • Early high strength & toughness • Used in thin concrete layers | • Loses strength in alkaline environments (needs special coatings) • Not for load-bearing structures |
Synthetic Fiber (PP, PET, etc.) | • Good for micro-crack control • Cheap, easy to mix • No rust, good dispersion | • Low tensile strength (fibers snap) • Makes concrete sticky, hard to compact • Not great for long-term durability |
Carbon Fiber | • Very strong & stiff • Bonds well with concrete • No rust, chemical-resistant | • Extremely expensive • Rarely used in large projects |
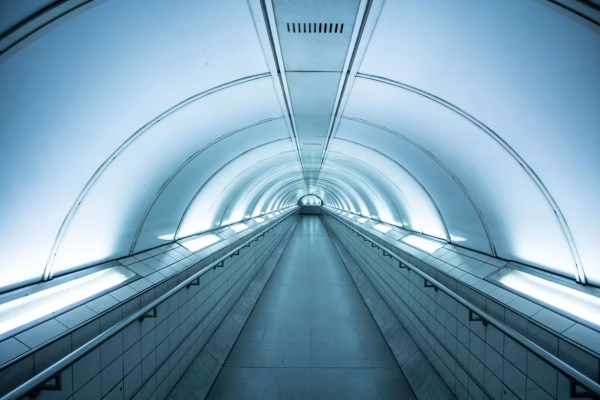
Applications for Fiber Reinforced Concrete
Steel Fiber Reinforced Concrete (SFRC)
1. Construction Projects
Floors, walls & structural components: Enhances tensile/flexural strength and impact resistance, reducing cracks and improving durability.
2. Roads & Bridges
Pavements & bridge decks: Withstands heavy loads and weather extremes, minimizing cracks for longer service life.
3. Hydraulic Structures
Spillways, sluices & dams: Boosts crack resistance and tensile strength for critical water infrastructure.
4. Repair & Reinforcement
Aging structure upgrades: Strengthens existing concrete to extend lifespan and load capacity.
5. Specialized Uses
Pipelines, inland waterways & blast-resistant structures: Performs reliably in demanding engineering scenarios.
Key Benefits: Unmatched toughness, crack control, and longevity for heavy-duty applications!
Glass Fiber Reinforced Concrete
1. Construction Industry
- Walls, roofs, and floors: Lightweight yet strong, reduce structural load while offering waterproofing and chemical resistance.
- Roof panels: Provides thermal insulation, soundproofing, and long-term weather resistance.
- Decorative elements: Used for facades, sculptures, and architectural details due to its smooth finish and design flexibility.
2. Roads & Bridges
- Bridge components: Corrosion-resistant, ideal for humid or chemically exposed environments.
- Tunnel linings: Enhances durability and waterproofing in underground structures.
- Road repairs: Quick crack-filling solution with high impact and rutting resistance.
3. Pipes & Drainage Systems
- Drainage pipes & manholes: Resists rust and chemical erosion, lighter than metal alternatives.
Key Benefits: Lightweight, strong, waterproof, and corrosion-resistant—ideal for aesthetic and long-lasting projects!
Polypropylene Fiber Reinforced Concrete
1. Building Construction
- Basements, water tanks, and roofs: Enhances waterproofing, reduces cracking, and improves freeze-thaw resistance.
- Mass concrete (e.g., high-rise foundations): Prevents thermal cracking and increases durability.
- Transfer slabs & beams: Ideal for extra-thick/large structural elements, improving crack resistance.
2. Civil & Hydraulic Engineering
- Roads & bridge decks: Resists fatigue and cracking, suitable for heavy-traffic areas.
- Dams, ports, aqueducts: Withstands seawater erosion and freeze-thaw cycles, extending service life.
3. Precast Concrete Products
- Pipes, blocks, prefab elements: Minimizes surface cracks and edge damage, boosts impermeability.
- Reinforcement protection: Reduces water penetration, preventing steel corrosion.
4. Ready-Mix Concrete
- Pumpable concrete: Improves workability, reduces bleeding, and prevents plastic shrinkage cracks.
- High-performance concrete (e.g., skyscrapers, long-span bridges): Enhances toughness, crack resistance, and ductility.
Key Benefits: Crack control, waterproofing, and durability—ideal for demanding environments!
Read More: Why use polypropylene fiber in concrete?
Final Words
Fiber-reinforced concrete is revolutionizing the construction industry by addressing the limitations of traditional concrete. With enhanced strength, crack resistance, and durability, FRC is ideal for demanding applications—from bridges and highways to precast architectural elements and blast-resistant structures.
At Mikem, we are a leading manufacturer of high-performance fibers for concrete, backed by over 20 years of industry expertise. With five advanced production facilities across China, we deliver consistent quality, innovation, and reliability to construction projects worldwide.
Our comprehensive fiber product line includes:
✔ Steel Fibers – Superior crack resistance & impact strength for heavy-duty applications
✔ Polypropylene (PP) Fibers – Excellent plastic shrinkage control & durability
✔ Plastic-Steel Fibers – Lightweight, corrosion-resistant solutions for architectural & precast concrete
✔ Polypropylene Fiber (Mesh) – Ultra-high strength for demanding structural reinforcement