Concrete is one of the most important materials in modern construction, and for good reason. From infrastructure megaprojects to factory flooring and residential buildings, concrete is a reliable, cost-effective, and adaptable solution trusted by engineers, contractors, and material specifiers worldwide.
At Mikem, we work closely with concrete producers and construction professionals, and we understand the importance of quality and performance on every job site. This article provides a clear, professional overview of what concrete is, how it’s made, its different types, and how it’s used across industries.
What is Concrete?
Concrete is a composite construction material made by mixing cement, water, aggregates, and sometimes admixtures. Once mixed, the paste undergoes hydration, a chemical reaction that causes it to harden and gain strength over time.
In practical terms, concrete starts as a workable mixture and becomes a solid material that can bear heavy loads, resist environmental stress, and maintain its form for decades.
Composition of Concrete
Understanding concrete’s composition is essential for manufacturers, contractors, and project engineers. Each component plays a critical role in performance:
1. Cement (10–15%): Acts as the binding material. Portland cement is the most commonly used type, which reacts with water to form a hardened matrix.
2. Water (15–20%): Triggers the hydration process and affects the concrete’s workability. Too much or too little water can reduce strength.
3. Fine Aggregates (25–30%): Usually sand, these particles fill voids between coarse aggregates, ensuring smooth finishing and better pumpability.
4. Coarse Aggregates (40–50%): Crushed stone or gravel gives concrete its bulk and improves strength and dimensional stability.
5. Admixtures (0–5%): Specialty additives are used to enhance or modify properties like setting time, air content, or chemical resistance.
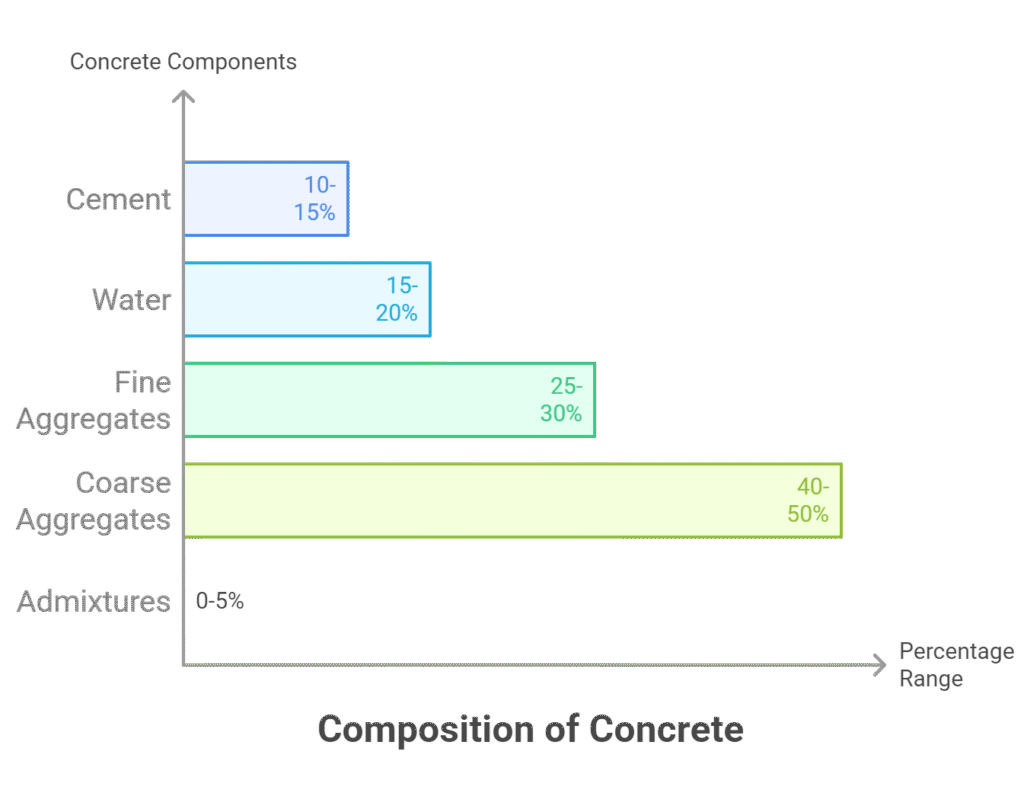
Types of Concrete
Concrete comes in a wide range of types tailored for specific applications.
1. By Strength
- Normal Strength Concrete (20–40 MPa): Commonly used in residential and light commercial structures.
- High Strength Concrete (40–80 MPa): Suitable for bridges, high-rises, and heavy-load applications.
- Ultra-High Strength Concrete (80 MPa+): Used in advanced structural elements requiring extreme performance.
2. By Density
- Lightweight Concrete (<1850 kg/m³): Ideal for reducing dead load in high-rise construction.
- Normal Weight Concrete (2200–2500 kg/m³): Standard for most structural applications.
- Heavyweight Concrete (>2500 kg/m³): Used in radiation shielding and specialized infrastructure.
3. By Reinforcement
- Plain Concrete: Used where tensile strength is not critical.
- Reinforced Concrete: Embedded with steel rebars to handle tension and bending.
- Prestressed Concrete: Pre-tensioned steel cables increase load-bearing capacity.
- Precast Concrete: Manufactured off-site for faster installation and consistent quality.
4. Specialty Types
- Self-Compacting Concrete (SCC): Flows without vibration—ideal for complex molds and dense reinforcement.
- Fiber-Reinforced Concrete (FRC): Enhanced with synthetic or steel fibers for improved toughness and crack resistance.
- Pervious Concrete: Allows water to pass through—perfect for sustainable urban drainage.
- Ready-Mix Concrete (RMC): Delivered in a ready-to-use state, reducing on-site labor and waste.
Properties of Concrete
Whether you’re designing for durability, strength, or sustainability, knowing the physical properties of concrete helps ensure the right mix for your project.
- Compressive Strength: The primary indicator of structural capacity, typically ranges from 20 to 80 MPa.
- Tensile Strength: Around 10% of compressive strength; often improved with reinforcement or fibers.
- Workability: Impacts ease of placement and finish. Key for large pours or intricate formwork.
- Durability: Resistance to weather, chemicals, abrasion, and freeze-thaw cycles.
- Thermal Properties: Acts as a thermal mass with low conductivity and moderate expansion.
- Permeability: Lower permeability enhances resistance to water penetration and corrosion.
- Setting Time: Initial set usually within 30–60 minutes; final set in 4–10 hours.
Common Uses of Concrete in Construction
Concrete is used in virtually every sector of construction. Its flexibility in design and performance makes it a preferred material across industries:
1. Buildings & Infrastructure
Used in structural components such as foundations, beams, columns, and slabs in residential, commercial, and industrial buildings.
2. Transportation
Vital for roads, highways, bridges, runways, and railway systems—offering strength, wear resistance, and long service life.
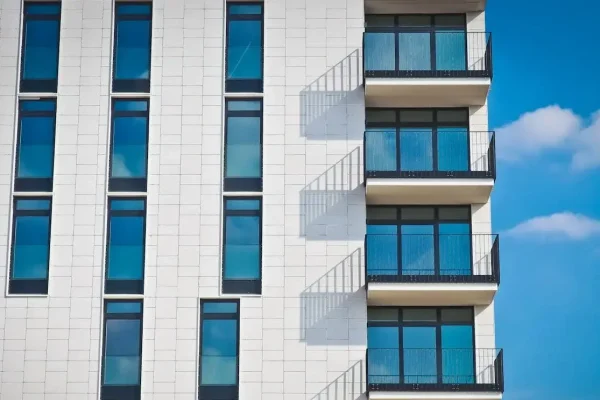
3. Water Management
From dams and reservoirs to canals and sewage plants, concrete offers strength and water resistance for critical infrastructure.
4. Marine & Offshore
Special mixes withstand saltwater corrosion and wave impact in ports, piers, and offshore platforms.
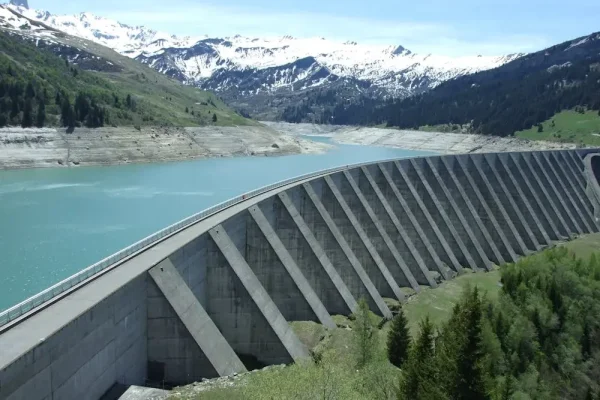
5. Urban Infrastructure
Sidewalks, curbs, parking lots, and stormwater systems rely on concrete’s durability and ease of maintenance.
6. Specialized Applications
Used in nuclear containment, precast elements, and decorative finishes in modern architectural design.
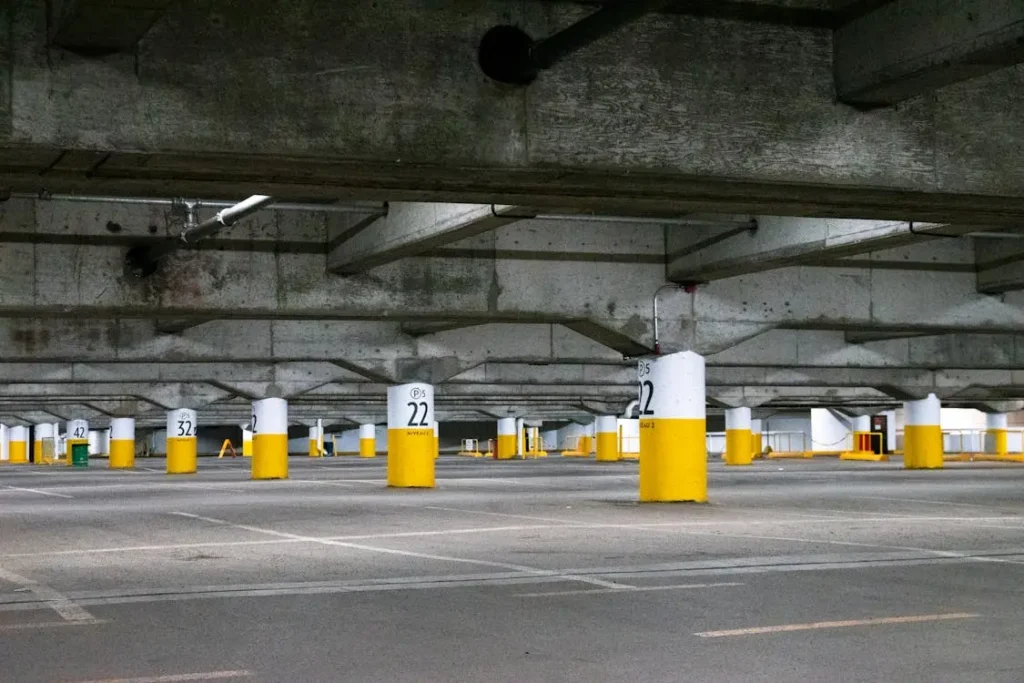
Enhance Performance with Mikem Concrete Additives
At Mikem, we offer a range of high-performance additives engineered to enhance concrete strength, durability, and workability for demanding applications:
- Polycarboxylate Superplasticizer: Improves flowability without increasing water content, enabling high-strength and self-compacting concrete.
- Polypropylene Fibers: Help control plastic shrinkage cracking and improve impact resistance in slabs, pavements, and precast products.
- Steel Fibers: Increase tensile strength and ductility, especially in industrial flooring, tunnel linings, and precast elements.
Final Thoughts
Concrete is more than just a building material—it’s the backbone of modern infrastructure. Selecting the right type of concrete with the right composition is essential to achieving performance goals, staying on budget, and ensuring long-term durability.
If you’re looking to optimize your concrete mix design for strength, durability, or sustainability, our technical team is here to support your next project. Contact Mikem today to learn how our advanced fiber additives and technical expertise can enhance your concrete performance.